Managing remote teams: Make work visible to seal process cracks
Nov 5, 2020
There are a number of things managers would rather not hear from a team member. High on that list must be:
“Oops. That one seems to have fallen through the cracks.”
What does it actually mean for something to “fall through the cracks”? And how can we manage the work our teams do so this happens less often?
This is the third post in a series on managing teams in our new remote or hybrid work environment. We have also shared tips on managing your communication channels and staying in sync across an organization. Although workers have always been susceptible to forgetting tasks, the additional communication challenges we work through during a crisis or disruption make any cracks in processes wider, deeper and more damaging.
What is a ‘crack'?
A crack is not some random event. From a process improvement perspective, there are ineffective patterns we frequently encounter. The most common is the “missed handoff.” Person A does their part and sends the project or task to Person B. Person B does their step, sends it to Person C and thinks they make it clear to Person C that it is now their responsibility.
However, Person C never gets the message and so the work sits abandoned in some mysterious inbox until a deadline has passed, the customer asks about it, or someone goes looking for a different file and stumbles upon the misplaced item.
Oops. It “fell through the cracks” because someone didn't know it was their turn to do the next step.
Building process awareness
The first step in addressing this kind of problem is to develop greater awareness in the team of what the work process actually is: to build a process map. Just as a road map shows how we are connected to our neighbors and how traffic normally flows, building a process map makes us more aware of how our work is connected to what our co-workers do.
Focus on the major steps. A process map differs from a standard operating procedure whose goal is to document every action taken so that another team member can accurately reproduce a specific task. In a process map, the goal is a high-level view that helps everyone see the complete chain of activities needed to get from a request to a final product or service delivered to the customer. Here are a few tips for building your process map.
- Make handoffs visible by using different colors to code different roles in the process. Don't forget handoffs with external partners, such as applicants and consultants or other work groups.
- Include approvals and technical review activities
- Look for places where the process stops or stalls. Is the wait time required, such as a public comment period, or is it caused by something else, such as requesting clarification from the applicant?
Mapping a process this way creates a great opportunity to ask what value each step adds to the overall process. In a previous post, we addressed that topic in greater depth.
With a clearer understanding of your process and the standard handoff points, you're ready to take the next step.
A key tool and how it works
We recommend a key tool called a “kanban board” or simply “kanban.” The term comes from Japanese and means “signal” or “signboard.” The goal of a kanban board is to make the status of every case in a process visible in a single view.
Each case is represented by a card with a small, standardized set of information, perhaps a case number, a simple name, and the next due date.
As a case moves through the process, its status is updated by moving the corresponding card down the kanban board. At a glance, you can see the status of all work in progress.
Staff and manager roles
Staff members have two main responsibilities when using a kanban: to consult the board to decide what case to work on next and to keep the status of every case up to date.
Managers should look for outliers and patterns.
Quickly scan the board. Are there cases that are falling behind or getting skipped over? These are indications that an additional resource is needed that you might be able to supply.
Is there a phase or status where cases are “bunching up?” Or are cases of a particular type moving more slowly than others? Maybe you have an opportunity for the team to improve the process as a whole.
The kanban becomes a key tool for managing the process as a whole for both day-to-day questions and for the broader strategic vision of continuous process improvement.
How do I get one?
For teams that involve at least some members working remotely, you'll need to enlist the help of your IT department to identify potential tools. A kanban interface might be available in software you already license. Or there could be off-the-shelf integrations that work with your current systems. There are also a large number of low cost, stand-alone kanban tools.
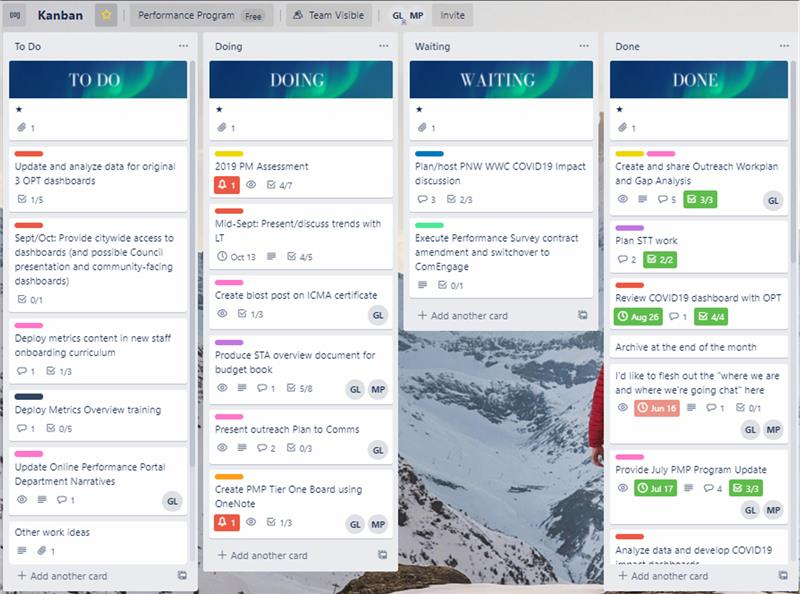
Courtesy of City of Bellevue
If your team is all in the office, many of the most effective kanbans we have seen have been a wall or whiteboard marked out with painter's tape and covered with sticky notes for each case-card. A low-tech solution might be all you need.
Consider the big picture
At its core, a kanban board is just a tool to “make work visible,” one of the core principles of Lean management. Work that “falls through the cracks” is just work that has stopped being visible. When work becomes visible, it becomes easier to manage and to improve.
We are here to help
The Center for Government Innovation is here to support your great public service – what people want, sooner, more accurately – and our services come at no additional charge to you. The Center provides technical assistance and process improvement facilitation to Washington governments. Because we specialize in working with local governments, we can tailor our services to fit your needs. Reach out to us at center@sao.wa.gov.